公司新聞
NEWS
熱門排行榜
HOT
聯(lián)系方式
CONTACT US
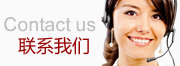
電話:0371-55682180
傳真:0371-55682180
手機:136-7371-1977
郵箱:3489671897@qq.com
地址:鄭州新密市超化鎮(zhèn)工業(yè)園區(qū)
編輯:admin
分類:耐火知識
發(fā)布:2018-06-20 10:00:03
瀏覽:次
高鋁磚產(chǎn)生裂紋的原因是多方面
分析了原料、泥料、成型、干燥、裝車、燒成等方面可能導致高鋁磚裂紋的原因以及相應的改善措施,高鋁磚產(chǎn)生裂紋的原因是多方面的,可能有一種或者幾種因素共同起作用,應結合實際采取針對措施,減少以致消除其危害,提高高鋁磚產(chǎn)品的合格率。
關鍵詞:高鋁磚;裂紋;二次莫來石化;壓裂
1 前言
高鋁磚是Al2O3含量在48%以上的硅酸鋁質制品[1],按照GB/T 2988—2004《高鋁磚》分類,高鋁磚按理化指標分為:LZ80、LZ75、LZ65、LZ55、LZ48共5個牌號[2],常用于砌筑高爐、熱風爐、電爐爐頂、鼓風爐、反射爐、水泥回轉窯內襯、玻璃熔窯的蓄熱室和風火隔墻[3]。在高鋁磚的生產(chǎn)過程中,因為產(chǎn)品表面和內部產(chǎn)生裂紋而造成的廢品是高鋁磚的主要廢品類型。在生產(chǎn)過程中,就要根據(jù)造成高鋁磚裂紋的各種因素進行調整改善,來降低高鋁磚裂紋發(fā)生的概率,提高高鋁磚產(chǎn)品的合格率。
2 裂紋原因分析及改善措施
2.1 原料原因及改善措施
生產(chǎn)高鋁磚用的主要原料高鋁礬土熟料的雜質(特別是K2O和Na2O)和燒結程度會使制品表面產(chǎn)生裂紋。燒結不良的熟料在制品燒成過程中繼續(xù)收縮且不均勻,引起制品開裂和產(chǎn)生裂紋;同時,在制品的燒成過程中,燒結不良的熟料本身的二次莫來石化(3α-Al2O3+2SiO2→3Al2O3·2SiO2,1 200~1 500℃)仍在繼續(xù)進行,二次莫來石化主要是指高鋁磚生產(chǎn)中結合黏土的SiO2與高鋁熟料的Al2O3反應生成莫來石,并伴隨體積膨脹(約10%),造成制品收縮不一致,導致了制品表面裂紋數(shù)量的增多和開裂程度的加大。
改善措施:高鋁磚的主要礦物組成為莫來石、剛玉和玻璃相。隨著制品中Al2O3含量的增加,莫來石和剛玉相的數(shù)量也增加,玻璃相相應減少,制品的耐火度和高溫性能隨之提高。實際生產(chǎn)高鋁磚時,要注意對所用的高鋁礬土熟料的雜質含量進行控制,按照YB/T 5179—2005《高鋁礬土熟料》的要求,K2O和Na2O含量≤0.35%~0.6%,盡量采用雜質含量低和燒結程度好的原料進行生產(chǎn)。
一般通過檢測熟料的吸水率來判斷熟料的燒結程度。生產(chǎn)過程中可以采用吸水率低的的熟料來生產(chǎn)高鋁磚,可以有效降低制品表面的裂紋。實踐表明,為了避免和減少高鋁磚表面網(wǎng)絡裂紋產(chǎn)生,對GL-50~GL-90高鋁礬土熟料的吸水率分別控制在2.5%~5.0%以下。
2.2 泥料原因及改善措施
泥料中的臨界顆粒尺寸、細粉加入量、泥料的混合質量都會影響高鋁磚半成品產(chǎn)生裂紋。如基質料一般由細粉組成,燒成過程中產(chǎn)生收縮,而顆粒一般是產(chǎn)生膨脹,兩者之間產(chǎn)生較大的變形差而引起內應力,從而使制品產(chǎn)生裂紋。
改善措施:高鋁磚泥料攪拌時,必須嚴格控制加料順序,混練時先加入顆粒料干混1~3 min,然后加入紙漿結合劑混練2~3 min,最后加入細粉混6~8 min,紙漿有效混練時間不低于10 min。鋁磚的泥料粒度常規(guī)控制參數(shù):3~2 mm,18%±5%;0.5~0.1 mm,15%±5%;<0.1 mm,40%±5%。水分含量<1.5%,實際生產(chǎn)時可以通過調整臨界顆粒尺寸、細粉加入量,同時可以引入適量的膨脹劑或者熱膨脹率較小的顆粒料,并制定合理的泥料控制參數(shù),以提高泥料的混合質量。
2.3 成型原因及改善措施
高鋁磚成型通常采用300 T以上摩擦壓力機或自動壓磚機成型。由于制品磚型、成型模具、布料不均、操作和壓力等原因造成的裂紋,最大特點是規(guī)律性強,裂紋的深度、位置、方向基本一致。
1)磚型的原因:由于不同磚型采用不同的模具進行壓制,帶孔、舌、槽或拐角的模具結構設計不合理,舌槽較多且多在模幫面上不易成型,且兩側模幫均為活板,出模后極易導致裂紋的產(chǎn)生。
2)成型模具設計不合理:由于成型模具設計缺少排氣槽、排氣孔,磚坯成型出模時易出現(xiàn)裂紋。
3)成型模具安裝和使用不合理:模具安裝不合理,磚坯成型出模時易出現(xiàn)裂紋。模具使用過程中,模具磨損后成型過程中模型與泥科相互磨擦,模壁表面的光潔度和硬度受到一定的磨損,易造成孔、舌、槽或拐角處出現(xiàn)裂紋。
4)布料不均的原因:布料不均,易使高鋁磚磚坯邊部與中間部位等的密實度不同,坯體在干燥過程中,因四周的密實度低于中間,邊部溫度高于中間溫度而導致邊部水分蒸發(fā)快,中間水分蒸發(fā)慢,形成邊部脫水率大于中部的狀況,當邊部脫水收縮過快時,坯體邊部即產(chǎn)生裂紋。
5)成型操作和成型壓力的原因:成型操作時,“短程快打”,“滿程狠打”,雖然大部分氣體被排除,但仍有一小部分氣體被壓縮未被完全排出,當此壓力超過磚坯的斷裂強度,就會造成磚坯產(chǎn)生內部橫向裂紋。
改善措施:
1)針對帶孔、舌、槽或拐角的磚型,可以設計合適的倒角和錐度參數(shù),壓制前模幫刷少量石墨和油的混合物,以方便磚出模,減低因模具結構設計不合理而產(chǎn)生的裂紋。
2)合理設計模具,在所有頂?shù)装鍌让婢庸? mm(寬)×1 mm(深)的排氣槽,排氣槽間距100 mm,以方便成型操作時氣體的排出,減少磚坯成型出模時出現(xiàn)裂紋。
除在模具上加工排氣槽外,所有產(chǎn)品在頂板面增設排氣孔,直徑Φ6 mm~Φ15 mm,沿長度方向間隔100~150 mm分布。長度≤230 mm,1個;230~400 mm,2個;>400 mm,3個。并在非工作面加工5 mm(寬)×2 mm(深)水平通道以利于排氣。通過采取以上改進措施,大大降低了磚坯成型壓制時產(chǎn)生的內部裂紋。
3)合理安裝成型模具,由專職模型質量質檢員負責模型現(xiàn)場檢查驗收,對模型進行磚型核對、尺寸測量,并對驗收情況一一記錄,同時加強對模具使用情況的檢查,對磨損程度較大的模具及時進行燒焊處理,降低因模具磨損而造成的半成品出模裂紋。對于磚型復雜的品種,可以通過模型改進等措施降低生產(chǎn)難度,提高生產(chǎn)效率和產(chǎn)品質量。
4)成型操作時,要注意均勻布料,使高鋁磚磚坯邊部與中間部位等的密實度基本相同,降低坯體在干燥過程中,因坯體部與中間部位密實度的不同而產(chǎn)生的裂紋。
5)成型操作時,按操作規(guī)程壓磚,先輕后重,緩慢加壓,保證打壓次數(shù),注意不要“短程快打”和“滿程狠打”,以減少內部裂紋的產(chǎn)生。
2.4 干燥原因及改善措施
由于坯體干燥敏感程度,干燥介質濕度、溫度、時間的不同會造成干燥時磚坯產(chǎn)生表面裂紋。磚坯干燥過程中,坯體中水分被蒸發(fā)的同時,體積也逐漸縮小。由于坯體干燥速度和收縮速度總是外快內慢,當其收縮量超過泥料的彈性系數(shù)(1%~2%)時,即產(chǎn)生網(wǎng)狀裂紋。
上一篇:不定形耐火材料
下一篇:玻璃熔窯冷卻和保溫的合理制度
相關資訊
- 水泥回轉窯的這幾個特殊部位,是耐火材料砌筑的關鍵 2023-12-09
- 澆注料、搗打料等不定形耐材的施工要點 2023-12-09
- 耐火磚的堆放技巧 2023-12-09
- 煉鋼用耐火材料 2023-12-09
- 教你耐火磚濕法砌筑的施工技巧 2023-12-09
- 玻璃池窯各部位所用耐火材料的應用情況分析 2023-12-09
- 陶瓷窯爐施工應注意的問題 2023-12-09
- 碳化硅的合成及碳化硅耐火材料的性能及用途 2023-12-09
- 煉鐵高爐內襯結構和原理 2023-12-09
- 沖天爐用耐火磚及澆注料類型 2023-12-09
推薦產(chǎn)品