公司新聞
NEWS
熱門排行榜
HOT
聯(lián)系方式
CONTACT US
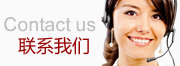
電話:0371-55682180
傳真:0371-55682180
手機(jī):136-7371-1977
郵箱:3489671897@qq.com
地址:鄭州新密市超化鎮(zhèn)工業(yè)園區(qū)
編輯:admin
分類:耐火知識(shí)
發(fā)布:2019-01-28 15:23:24
瀏覽:次
硅磚是主要由鱗石英、方石英以及少量殘余石英和玻璃相組成的酸陛耐火材料,對(duì)酸陛爐渣抵抗能力強(qiáng),但會(huì)被堿性渣侵蝕,不耐Al2O3、K2O、Na2O等氧化物侵蝕,它的荷重軟化溫度高,介于1640~1680℃之間,與鱗石英、方石英熔點(diǎn)(分別為1670℃和1713℃)接近,最大的缺點(diǎn)是熱震穩(wěn)定性低,但耐火度與荷重軟化溫度相近,在高溫下長(zhǎng)期使用不變形,有利于保證砌筑體在使用時(shí)的結(jié)構(gòu)強(qiáng)度。
硅磚主要用于煉焦?fàn)t的炭化室和燃燒室的隔墻,均熱爐、熱風(fēng)爐、酸性平爐和玻璃窯爐的爐頂或拱頂?shù)炔课弧,F(xiàn)今在煉鐵技術(shù)方面,直接還原與融熔還原煉鐵新技術(shù)正在逐步轉(zhuǎn)化為生產(chǎn)力,而在煉焦工業(yè),已研制出一種不用焦?fàn)t生產(chǎn)的“成型焦炭”,可以替代一部分傳統(tǒng)焦炭。隨著這些新技術(shù)的推廣,硅磚的需要量將逐步減少。然而,在國(guó)內(nèi)外玻璃窯上,硅磚除了在蓄熱室格子體和部分胸墻部位被其它磚替代外,在熔窯碹頂,硅磚仍保持其優(yōu)勢(shì)地位。
硅磚同大多數(shù)燒結(jié)耐火磚一樣均采用半干法生產(chǎn)制品、隧道窯燒成,它在生產(chǎn)過(guò)程中出現(xiàn)裂紋是導(dǎo)致其廢品率提高的主要原因之一。本文對(duì)硅磚成品的裂紋類型和成因進(jìn)行分析,說(shuō)明通過(guò)嚴(yán)格控制硅磚生產(chǎn)主要的機(jī)壓成型和燒成工藝環(huán)節(jié),能減少硅磚裂紋形成,并顯著提高產(chǎn)品質(zhì)量。此經(jīng)驗(yàn)對(duì)其它燒結(jié)耐火材料的生產(chǎn)也有借鑒作用。
硅磚裂紋的類型
硅磚制品的裂紋可分為表面裂紋和內(nèi)部裂紋,后者也稱為層裂。表面裂紋又分為橫向裂紋、縱向裂紋和網(wǎng)狀裂紋。硅磚是采用半干料機(jī)壓成型方法制備致密坯體的,沿磚坯加壓方向產(chǎn)生的裂紋為橫向裂紋,垂直于磚坯的加壓方向產(chǎn)生的裂紋為豎向裂紋,而硅磚制品表面由數(shù)條裂紋組成的,呈蛛網(wǎng)狀分布的裂紋,即網(wǎng)狀裂紋,參見(jiàn)圖1。
圖1 硅磚表面裂紋類型
通常,就一塊標(biāo)準(zhǔn)型硅磚而言,其坯體加壓方向一般為厚度方向。硅磚制品的成型過(guò)程,實(shí)質(zhì)上是一個(gè)使坯料內(nèi)顆粒密集和空氣排出、形成致密坯體的過(guò)程。磚坯經(jīng)機(jī)壓成型后,具有密度高、強(qiáng)度大、干燥收縮和燒成收縮小、制品尺寸容易控制等優(yōu)點(diǎn)。但是,當(dāng)機(jī)壓成型工藝控制不當(dāng),坯體在加壓過(guò)程中會(huì)形成的垂直于加壓方向的層狀裂縫,因此,硅磚內(nèi)部的層狀裂縫或者簡(jiǎn)稱層裂,亦是縱向裂紋。
大的層裂在磚坯剛成型,或磚坯干燥后就可檢測(cè)出來(lái)。但磚坯中微小層裂,只有在硅磚燒成過(guò)程中隨熱應(yīng)力的作用繼續(xù)擴(kuò)展,才能在燒后明顯地被檢測(cè)出來(lái)。含有裂紋缺陷尤其是層裂的硅磚容易發(fā)生斷裂,既不能使用,又降低了硅磚制品的成品率。
硅磚裂紋形成和預(yù)防的主要措施
機(jī)壓成型
硅磚的層裂主要由于機(jī)壓成型工藝控制不當(dāng)造成,所以有時(shí)也稱之為機(jī)壓裂紋。硅磚的坯料和磚坯,都是由固體、水或其它結(jié)合劑和空氣三相物質(zhì)共同組成的。在整個(gè)機(jī)壓成型或稱為模壓成型過(guò)程中,固相和液相量沒(méi)有改變,而坯料中空氣的數(shù)量則由于壓力的作用被壓縮和減少,被壓縮的坯料容積亦相應(yīng)減少。模壓成型過(guò)程大致可分為以下三階段。
第一階段,在壓力的作用下,坯料中的顆粒開(kāi)始移動(dòng),重新配置成較緊密堆積。該過(guò)程的特點(diǎn)是壓縮明顯。當(dāng)壓力增至某一數(shù)值后,進(jìn)入第二階段。
第二階段,顆粒發(fā)生脆性及彈性變形,坯料被壓縮到一定程度后,即阻礙進(jìn)一步壓縮。當(dāng)壓力增加,達(dá)到使顆粒再度發(fā)生變形的外力時(shí),引起坯料的再壓縮,坯體致密度隨之增加。這個(gè)階段是壓縮及增壓變得短促而頻繁的階段。
第三階段,在極限壓力下,坯料的相對(duì)致密度基本穩(wěn)定,難以提高。磚坯的模壓成型結(jié)束。在模壓成型過(guò)程中,必須將彈性后效所造成的坯體滯后膨脹量控制為2%以下,否則往往在壓制過(guò)程中直接造成廢品。如果沿磚坯加壓方向坯體形成“層密度”,密度差大于2%,磚坯內(nèi)部就容易產(chǎn)生層狀裂紋的缺陷,使得磚坯在燒成過(guò)程中熱膨脹不均而產(chǎn)生較大的熱應(yīng)力,形成平行于密度層的縱向裂紋以致報(bào)廢。
壓制硅磚時(shí)宜用長(zhǎng)徑比小的短模,不宜采用長(zhǎng)徑比大的高模,來(lái)提高坯體內(nèi)壓力分布的均勻性。同時(shí),采取向坯料中引入某些塑化劑及表面活性劑,降低坯料內(nèi)摩擦,減少壓力傳遞損失;提高模具的光潔度或?qū)δW油坑?,降低坯料外摩?采用雙面壓制,降低坯體L/D比值;采用多次加壓,先輕后重方式,避免磚坯內(nèi)壓力不致積蓄過(guò)大及消除彈性后效等技術(shù)措施,提高磚坯內(nèi)部壓力與密度的均勻性。從而,避免硅磚坯體中距受壓面近的地方密度大,距受壓面遠(yuǎn)的地方密度小,以減少層密度形成導(dǎo)致裂紋缺陷的產(chǎn)生。
此外,硅磚坯料是由骨料、熟料、球磨粉、礦化劑、亞硫酸紙漿廢液及增塑劑經(jīng)混練制備而成,改善坯料的捏練工藝,也有助于提高磚坯的密度。從物體混合技術(shù)而言,使物料同相之間發(fā)生移動(dòng)叫混合,異相之間的移動(dòng)叫攪拌,而將高黏度液體與固體相互混合的操作叫捏練(捏合與混練)。通過(guò)合理捏練,可以完成細(xì)粉對(duì)大顆粒的包覆,有效排除氣體,提高坯料致密化程度,從而降低磚坯氣孔率。
硅磚的燒結(jié)實(shí)際上是SiO2的同質(zhì)多晶轉(zhuǎn)變過(guò)程,硅石原料在礦化劑作用下,經(jīng)緩慢燒成,基本上轉(zhuǎn)化為鱗石英、方石英,僅有少量殘余石英。硅磚在使用中加熱到1450℃時(shí)有1.5%~2.2%的總體積膨脹,這種殘余膨脹會(huì)使砌縫密合,有利于保證硅磚砌筑體呈現(xiàn)良好的緊密性和結(jié)構(gòu)強(qiáng)度。而且這種SiO2的同質(zhì)多晶轉(zhuǎn)變,決定了烤窯前期階段耐火材料監(jiān)控的重點(diǎn)是硅磚,升溫速率以慢速均勻?yàn)樘卣?。硅磚在150~300℃溫度范圍內(nèi),由于其中β、α-方石英的晶型轉(zhuǎn)變伴隨較大的體積效應(yīng),在烤窯時(shí)應(yīng)特別注意在此溫度范圍內(nèi)進(jìn)行緩慢升溫。
石英轉(zhuǎn)變?yōu)轺[石英的轉(zhuǎn)化速度和程度,不僅與溫度的高低和礦化劑的存在有關(guān),而且也與溫度的作用時(shí)間、原料的顆粒大小、轉(zhuǎn)化相結(jié)晶大小等因素有關(guān)。溫度高、高溫作用時(shí)間長(zhǎng)、顆粒小、結(jié)晶小、礦化劑作用強(qiáng),則轉(zhuǎn)化快,反之則慢。硅磚的主晶相為鱗石英和方石英,鱗石英熔點(diǎn)1670℃,具有較高的體積穩(wěn)定性。如果硅磚中鱗石英呈矛頭狀雙晶形態(tài)相互交錯(cuò)為網(wǎng)絡(luò)狀分布,能夠使硅磚具有較高的荷重軟化點(diǎn)及機(jī)械強(qiáng)度。當(dāng)硅磚中殘余石英較多時(shí),由于在使用中它會(huì)繼續(xù)進(jìn)行晶型轉(zhuǎn)變,體積膨脹較大,會(huì)導(dǎo)致磚體結(jié)構(gòu)松散開(kāi)裂。硅磚在燒成過(guò)程中發(fā)生的物理一化學(xué)變化可歸納如下:
?、?lt;150℃排除磚坯的殘余水分。
?、?50—550℃時(shí)Ca(OH)2開(kāi)始分解,550℃分解完畢,此時(shí)硅磚顆粒之間的結(jié)合由于CaO等作用而破壞,強(qiáng)度下降,坯體變脆。
?、?50~650℃時(shí),β一石英磚轉(zhuǎn)化為一石英,體積膨脹。
?、?00~700℃時(shí),CaO與SiO2之間發(fā)生固相反應(yīng),坯體強(qiáng)度提高。
⑤800~1100℃時(shí),磚坯出現(xiàn)液相反應(yīng),坯體強(qiáng)度迅速增加。從1100℃開(kāi)始,石英的轉(zhuǎn)化速度大為增加,這時(shí)低比重石英變體,產(chǎn)生較大體積膨脹。
⑥1300~1350℃時(shí),由于鱗石英和方石英數(shù)量增加,坯體真比重降低,同時(shí)體積膨脹加大有可能導(dǎo)致開(kāi)裂。
?、?350~1470℃時(shí),石英的轉(zhuǎn)化程度和由此產(chǎn)生的膨脹很大,僅一石英、亞穩(wěn)定方石英和礦化劑及雜質(zhì)等相互作用形成液相,并侵入石英顆粒在形成亞穩(wěn)定方石英時(shí)出現(xiàn)裂紋中,促進(jìn)了一石英和亞穩(wěn)定方石英不斷地熔解于所形成的液相中,使之成為硅氧的過(guò)飽和熔液,然后以穩(wěn)定的鱗石英形態(tài)不斷地從熔液中結(jié)晶出來(lái)。此時(shí)液相粘度愈大,硅磚轉(zhuǎn)化速度愈快,磚坯產(chǎn)生裂紋可能性愈大。
因此,為防止硅磚在燒成過(guò)程中發(fā)生晶型變化,伴隨較大的體積變化導(dǎo)致裂紋的形成,必須采取以下工藝措施:
要控制燒成不同溫度范圍的升溫速率。小于600℃升溫速率放慢,600~1000℃時(shí)升溫速率可加快,1100~1300℃時(shí)升溫速率應(yīng)緩慢,1300℃~燒成溫度(1430℃至1450℃)時(shí),升溫速率應(yīng)是燒成過(guò)程中最慢的。燒成后的硅磚冷卻時(shí)在600℃以下,特別在300℃時(shí)應(yīng)緩慢。這樣可以有效緩沖晶型轉(zhuǎn)變的體積變化,使其鱗石英及方石英含量較高,并避免裂紋的形成。
應(yīng)在高溫?zé)呻A段采用還原氣氛,有利于低價(jià)氧化鐵的礦化作用和促進(jìn)鱗石英大量生成。否則,在氧化氣氛下尤其礦化劑不足時(shí),α-石英大多數(shù)轉(zhuǎn)化為α-方石英,這種轉(zhuǎn)變稱為“干轉(zhuǎn)化”。在干轉(zhuǎn)化時(shí),由于磚體不均勻的體積膨脹很大,而又無(wú)液相緩沖應(yīng)力,會(huì)導(dǎo)致制品結(jié)構(gòu)松散和開(kāi)裂。同時(shí),應(yīng)在硅磚燒成的不同溫度階段進(jìn)行適當(dāng)保溫,使硅磚具有合理相組成,滿足使用要求。
改善半成品裝車制度,降低裂紋發(fā)生的概率。硅磚的橫向裂紋,即平行于制品的加壓方向裂紋(圖1),通常為制品燒成時(shí)各部分受熱不均所致,它們多出現(xiàn)在磚垛外側(cè)的受火面,特別是頂層的制品表面。而硅磚表面網(wǎng)狀裂紋,除了由于捏練不勻或原料變化,使得坯體本身微觀不均勻的起因外,通常是由于制品受熱溫度過(guò)高且起伏較大所致。在裝車時(shí),需要將特異型硅磚放置于窯車的內(nèi)部,標(biāo)準(zhǔn)普通型磚裝在窯車的外部;異型磚的凸出部位或易出現(xiàn)裂紋的部位向里;窯車頂部要覆蓋一些薄片磚,以避免火焰的直接沖擊等措施,否則將會(huì)導(dǎo)致裂紋增多。
結(jié) 語(yǔ)
裂紋是影響硅成品率及性能的主要因素之一,抓住機(jī)壓成型和燒成工藝是避免硅磚裂紋形成的關(guān)鍵。硅石原料的理論和實(shí)際轉(zhuǎn)化情況有所不同,需根據(jù)原料、磚型種類等變化實(shí)時(shí)地調(diào)整其燒成制度。硅磚坯料的制備和質(zhì)量是重要的,甚至是關(guān)鍵的因素,只有嚴(yán)格控制好每一道工藝環(huán)節(jié),方能高效低耗地產(chǎn)生性能良好的硅磚產(chǎn)品。
相關(guān)資訊
- 水泥回轉(zhuǎn)窯的這幾個(gè)特殊部位,是耐火材料砌筑的關(guān)鍵 2023-12-09
- 澆注料、搗打料等不定形耐材的施工要點(diǎn) 2023-12-09
- 耐火磚的堆放技巧 2023-12-09
- 煉鋼用耐火材料 2023-12-09
- 教你耐火磚濕法砌筑的施工技巧 2023-12-09
- 玻璃池窯各部位所用耐火材料的應(yīng)用情況分析 2023-12-09
- 陶瓷窯爐施工應(yīng)注意的問(wèn)題 2023-12-09
- 碳化硅的合成及碳化硅耐火材料的性能及用途 2023-12-09
- 煉鐵高爐內(nèi)襯結(jié)構(gòu)和原理 2023-12-09
- 沖天爐用耐火磚及澆注料類型 2023-12-09
推薦產(chǎn)品